
Detailed measurements of droplet size distributions were carried out using laser shadowgraphy, along with high speed flow visualization.

The nozzle establishes a countercurrent flow configuration in which the gas and liquid are directed in opposite directions, establishing a two-phase mixing layer. The simulation reveals the detailed process of self-sustained flow oscillations and the physical mechanism that generate liquid filaments and final droplets.Ībstract = "We study the enhanced atomization of viscous liquids by employing a novel two-fluid atomizer. To gain insight into the mixing process inside the nozzle, simulations are carried out using an Eulerian-Eulerian Volume of Fluid (VoF) approach for representative experimental conditions. The counterflow nozzle produces a spray whose characteristics are relatively insensitive to fluid viscosity over the range studied, for gas-liquid mass flow ratios between 0.25 and 1. The performance of this nozzle is compared to the ‘flow-blurring’ nozzle studied by other investigators for four test liquids of viscosity ranging from 1 to 133.5 mPa.s. The measurements suggest that the liquid emerges as a spray with little further secondary atomization. Want to know more about the characteristics of a good lubricant? We cover all bases, and more in ‘A Complete Guide to Lubricants - Types, Quality & Testing’.We study the enhanced atomization of viscous liquids by employing a novel two-fluid atomizer. A “good” lubricant should meet all advertised parameters and performance promises, as well as offer value for money. Good value for moneyĬost is a major factor when choosing mechanical lubricants, particularly in the face of economic volatility.
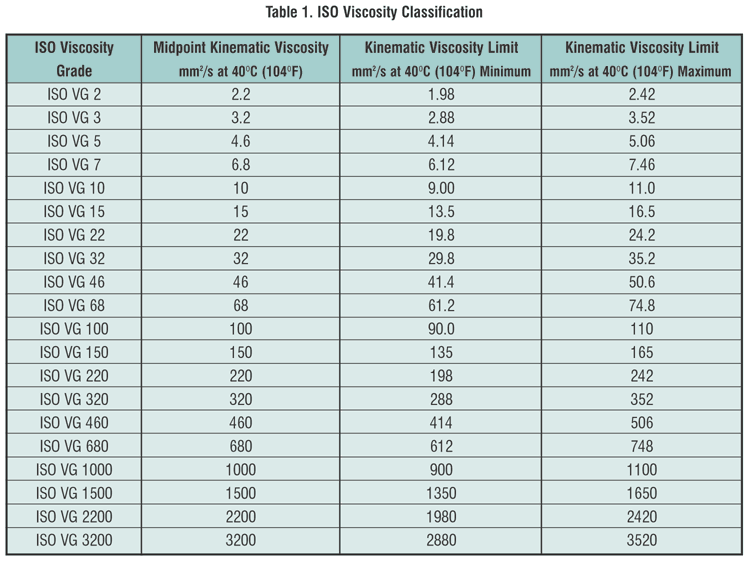
Lubricants with high oxidation and corrosion resistance are coveted by operators as they help prevent these issues, which can compromise performance, shorten the lifespan of assets and result in catastrophic failure. Oxidation and corrosion are two of the biggest threats to mechanical performance.
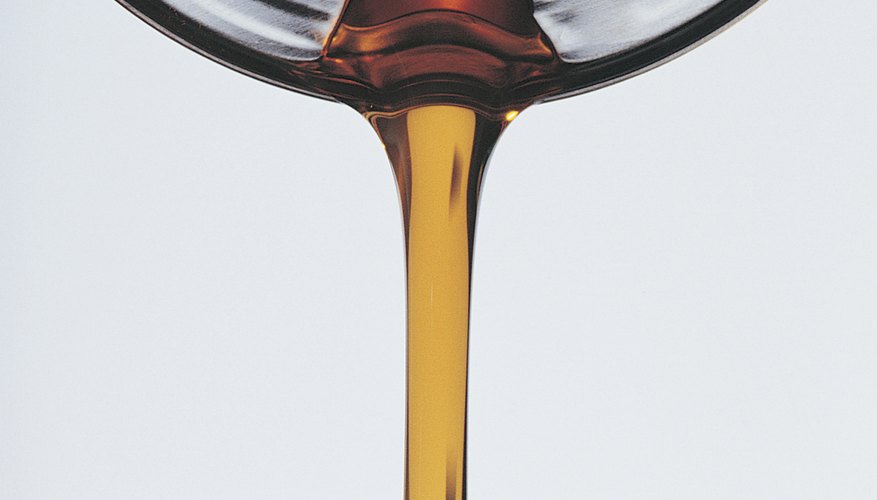
Lubricants with good a demulsibility rating can easily release water, which helps prevent H2O contamination. This can lead to issues such as contamination from abrasive wear particles, excessive energy consumption due to increased resistance and overheating caused by friction. Water can drastically compromise the performance of lubricants, preventing them from forming a protective barrier between moving parts. High viscosity lubricants are usually oil-based and are often enhanced with additives to boost performance. This is because high viscosity lubricants disperse more easily and can be easily distributed to all moving parts in mechanical system. Generally, lubricants with a high viscosity index are more desirable than their counterparts with low viscosity. Kinematic viscosity describes the rate at which the lubricant flows under gravity and is a key parameter used to determine the quality of lubricants. For example, overheating caused by a cooling system leak. These characteristics help them to stay in a liquid state and make them less likely to fail in the face of less-than-ideal operating conditions.
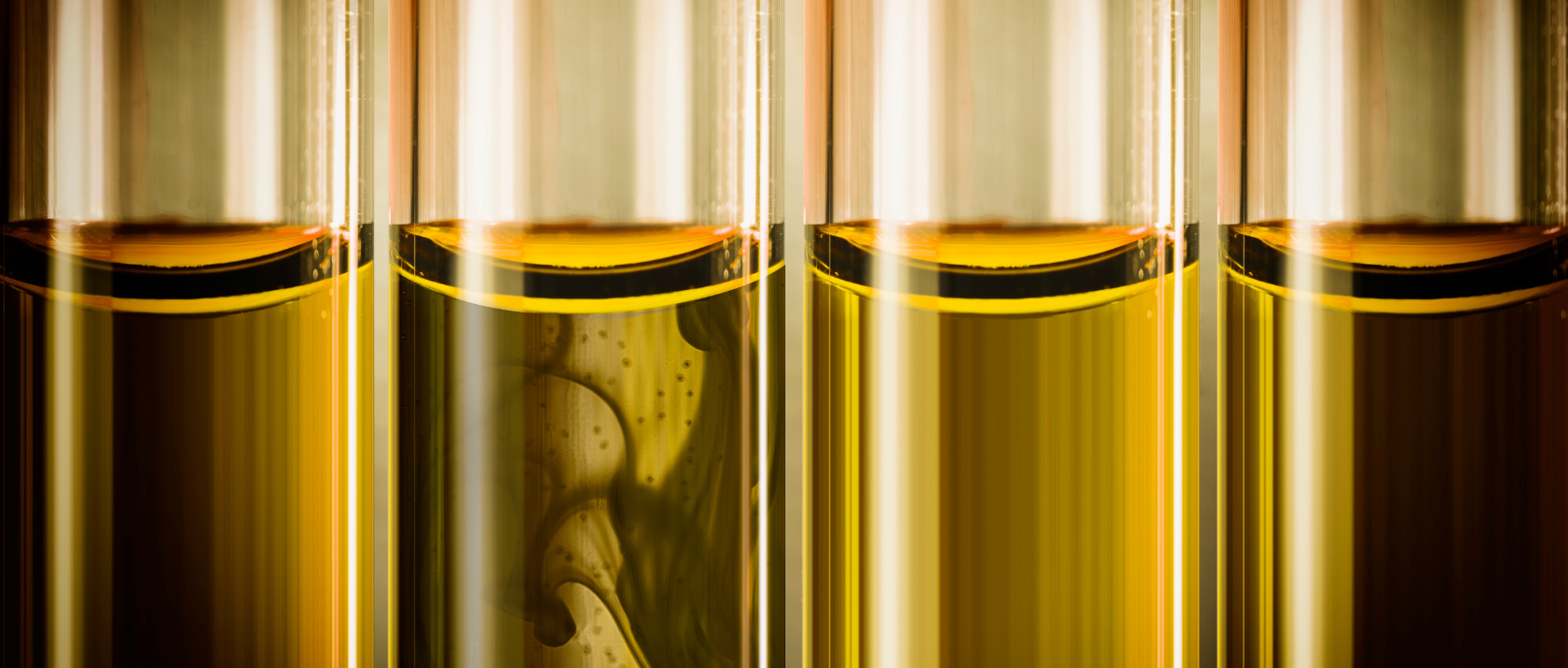
Lubricants with high boiling points and low freezing points are considered more useful as they’re functional across a wide range of temperatures. These include the following: High boiling point and low freezing point That said, there are some key traits that most high-quality lubricants share. For example, a jet engine will require a different lubrication strategy to a hydraulic pump system used at an oil refinery. So, what are the characteristics of a good lubricant? The answer depends heavily on the application the lubricant is being used for. Choosing a good lubricant is a critical part of any asset management and maintenance strategy. Lubricants are the lifeblood of mechanical assets, forming a protective layer between moving parts to minimise friction, maintain productivity and prevent unplanned downtime.
